Coca-Cola favours Tanner OHT

Coca-Cola Hellenic favours the Tanner clamping conveyor
Since March 2013, Coca-Cola HBC Austria has been using Tanner’s new technology. At the bottling plant in Edelstal, Austria, Coca-Cola Hellenic installed Tanner’s new OHT clamping conveyor. Installed directly upstream of the blow moulding machine, in one phase the PET preforms are conveyed overhead, blown out with air and any foreign particles are removed by suction. The cleaning efficiency is unrivalled anywhere in the world. The Coca-Cola Hellenic Group set a clear example in the field of quality improvement with this installation.
Following a presentation of the new technology in December of last year and pre-validation at Tanner, the project was implemented just three months later. At the bottling plant in Edelstal, Vienna, the existing Tanner preform feeding system was modified and the OHT clamping conveyor was installed as a component of the Ultra-Clean line for mineral water. “We have been impressed by the quality of the product, as well as Tanner’s service,” explains Patrick Misch, Supply Chain Director. In Edelstal, Coca-Cola HBC Austria operates a bottling plant for soft drinks such as Coca-Cola, Diet Coke, Fanta and Sprite, as well as the mineral water Römerquelle. The company is part of the Coca-Cola Hellenic Group, one of the world’s largest bottlers of products from The Coca-Cola Company, and the largest in Europe. In Austria alone, Coca-Cola Hellenic supplies 8.4 million people with their quality products. The Coca-Cola Hellenic Group operates in 28 countries and supplies over 581 million people.
Ultra-Clean line for bottling Römerquelle mineral water
Since April 2012, the Coca-Cola site in Edelstal has been in possession of a PET Ultra-Clean line for bottling mineral water and flavoured water under the Römerquelle brand name. At a rate of 28,000 bottles per hour, bottling is carried out using the three-shift system to the highest standards of hygiene. With the installation of the Tanner clamping conveyor in March 2013 and the associated efficient preform cleaning upstream of the blow moulding machine, it was possible to upgrade the Ultra-Clean line with a further quality product. This is another reason that this bottling line stands out not only at the Edelstal site but also within the Coca-Cola Hellenic Group.
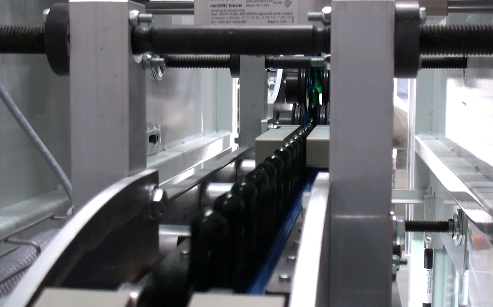
Efficient preform internal cleaning system upstream of the blow moulding machine
Along the Ultra-Clean line, the preforms for the 0.33-litre, 0.5-litre and 1.0-litre bottles are cleaned using the new Tanner product and fed to the blow moulding machine. The clamping conveyor is an attractive proposition because of its overhead preform guidance system. During the overhead phase, the preforms are blown out by two ionising nozzles and four air nozzles. At the same time, any foreign particles are removed from the preforms by suction. The cleaning efficiency is impressive and is unrivalled anywhere in the world.
Collaboration as a win-win situation for everyone involved
The project turned out to be a win-win situation for both Coca-Cola Hellenic and Tanner. Tanner was able to apply its many years of experience in the internal cleaning of preforms, as well as support Coca-Cola Hellenic in drawing up the specification for the internal cleaning of preforms. On the other hand, experimental values from Coca-Cola Hellenic’s production plant were equally influential in shaping the product. Marco Tanner, CEO of M. Tanner AG, says: “The constant exchange of experience and ideas with our customers is incredibly important. Here, together with the customer we are laying the foundation stone for long-lasting and successful collaboration.”
Camera inspection and UVC irradiation is also possible
In addition to the preform internal cleaning system, the clamping conveyor can also be equipped with camera inspection and a UVC irradiation unit. Camera inspection allows the preforms to be checked for deformations on their opening, support ring fractures and out-of-roundness. Automatic ejection allows production to be maintained continuously. The UVC irradiation unit at the clamping conveyor output can be used for destroying germs on the thread and opening of the preform.