OHT retrofit at Möhl

The Swiss drinks manufacturer Möhl upgrades its PET bottling line with the Tanner clamping conveyor
Mosterei Möhl is increasing the quality of its products by installing the Tanner clamping conveyor. The PET preforms (PET blanks) are now conveyed overhead in one phase, upstream of the stretch blow machine, and blown out with ionised air. This method noticeably increases product safety. By installing the new Tanner technology, Mosterei Möhl has chosen an extremely efficient preform cleaning method and sets a clear example in the area of quality development.
Mosterei Möhl – Drinks manufacturer for over 100 years
The tradition of using fruit goes back four generations at Mosterei Möhl, which is based in the Swiss town of Arbon near Lake Constance. In 1895, Hans Georg Möhl opened the Rössli guest house with the first juice cellar. From this point onwards, the Möhl family also began to sell fermented apple juice to other restaurants. Over the years, the manufacturer of fruit-based drinks grew continuously and expanded its range of apple ciders and juices. Today, between 13,000 and 26,000 tonnes of cider fruits are pressed at Möhl, depending on the size of the harvest. At the bottling plant in Arbon, the manufacturer of fruit-based drinks produces thirteen different types of apple ciders and juices. The product range includes SHORLEY, which is very popular in Switzerland.
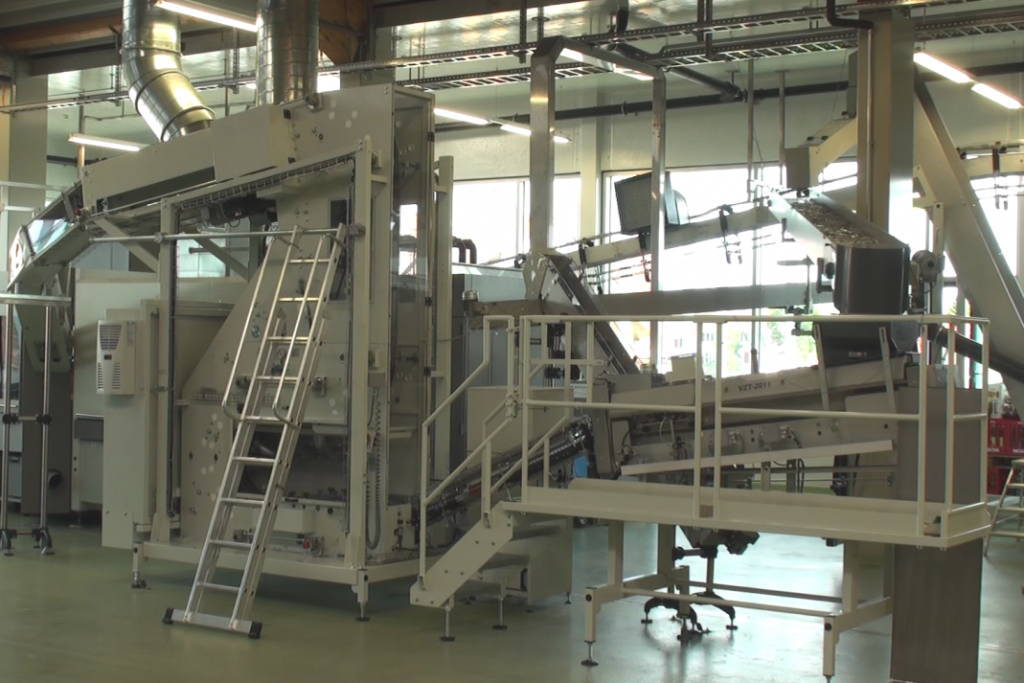
Two production lines
In addition to its own juice and distillery museum and a cash-and-carry store, Mosterei Möhl has two production lines for bottling in PET and glass bottles. The bottling line for PET bottles works with an output of 20,000 0.5-litre PET bottles an hour, or 10,000 1.5-litre PET bottles an hour, using a single-shift system. Two operators operate the PET line.
Traditional line for bottling PET bottles
Mosterei Möhl has had a bottling line for PET bottles since 2008. The bottling line consists of a traditional PET line with a stretch blow machine, followed by an air conveyor, filler and capper for bottles. With the integration of the OHT clamping conveyor, and the associated efficient cleaning of the preforms, Mosterei Möhl can ensure that any foreign particles are removed upstream of the blow moulding machine. Lukas Möhl, Head of Engineering and Maintenance at Mosterei Möhl AG, says: “We were looking for an efficient preform rinser for our PET line. With the Tanner clamping conveyor, we found the perfect concept and product for our line. We are extremely pleased with the production and cleaning efficiency of the system.”
Overhead air rinser upstream of the stretch blow machine
For bottling in 0.5-litre and 1.5-litre PET bottles, the PET preforms are cleaned using the new Tanner technology and fed directly to the stretch blow machine. Thanks to the overhead guidance system, the preform cleaning efficiency is unrivalled anywhere in the world. During the overhead phase, the preforms are blown out with ionised air and, at the same time, any foreign particles or dust particles are removed by suction.

Compatible with the previous generation of Tanner preform feeding system
By integrating the OHT clamping conveyor into the existing Tanner preform feeding system, the silo belt, the elevator, various conveyor belts and the roller sorter were able to be used again. Marco Tanner, CEO of M. Tanner AG, says: “The OHT clamping conveyor is compatible with the previous generation of Tanner systems. This enables us to upgrade the existing Tanner feeding system with the new technology without any problems.” The compatibility with the previous generation means that the roller sorter and the OHT clamping conveyor can be operated using the same control system. The on-site system conversion was carried out by the Tanner service team.
Camera inspection and UVC-irradiation options
In addition to the preform internal cleaning system, the clamping conveyor can also be equipped with camera inspection and a UVC-irradiation unit. The integrated camera inspection makes it possible to check the quality of the preforms. The preforms are checked for deformations on their opening, support ring fractures and out-of-roundness. Thanks to automatic ejection, the defective preforms are separated out without needing to stop production. The UVC-irradiation unit at the clamping conveyor output can be used for destroying germs on the thread and opening of the preform. The Tanner clamping conveyor, the all-in-one solution close to the floor.